or call: +1 (845) 347-8894
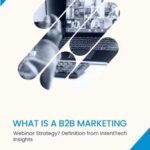
or call: +1 (845) 347-8894
How do you serve markets too small for mass production but too complex for traditional prototyping? For decades, niche industries have struggled to find cost-effective, scalable ways to develop products tailored to specific user needs. Today, that challenge is being met by a transformative technology – 3D printing.
Once limited to rapid prototyping, 3D printing, or additive manufacturing, it now plays a central role in delivering highly customizable products across niche sectors. With its ability to reduce waste, lower costs, and accelerate design-to-delivery cycles, this technology is enabling innovation at scales previously considered unfeasible.
In traditional manufacturing, customization often comes at the expense of scale or cost-efficiency. Tooling and mold changes are expensive and time-consuming, especially when production volumes are low. Niche industries, such as medical prosthetics or aerospace components, frequently require custom parts for every customer or mission. 3D printing eliminates these trade-offs by removing the need for specialized tooling.
According to a report by Statista, the global 3D printing market is projected to reach $56.2 billion by 2028, up from $20.37 billion in 2023, showing widespread adoption and growing trust in this method. Much of this growth is fueled by its value in industries with specific, non-generic needs.
By allowing for on-demand customization, 3D printing empowers companies to innovate without minimum order quantities or inventory storage challenges. This is particularly crucial for markets where demand is unpredictable or where each customer requires a unique solution.
Perhaps no industry better illustrates the potential of 3D printing for customization than healthcare. From patient-specific implants to dental devices and surgical tools, additive manufacturing is helping practitioners tailor solutions to individual anatomies.
One notable example is the production of 3D-printed titanium spinal implants, customized based on CT scans of individual patients. These implants match the patient’s vertebral geometry, enhancing surgical outcomes and reducing recovery time.
A 2023 study published in Nature Biomedical Engineering found that 3D-printed orthopedic implants reduce surgical time by 20% and increase implant fit accuracy by over 95%, leading to fewer complications and improved patient outcomes.
In prosthetics, startups like Unlimited Tomorrow are leveraging 3D printing to offer low-cost, custom-designed prosthetic arms that are lightweight, highly functional, and manufactured at a fraction of traditional costs. This democratizes access to essential medical devices, especially in underserved regions.
The aerospace industry thrives on precision and weight optimization. Here, 3D printing supports the creation of intricate, lightweight parts designed for specific aircraft models or space missions.
NASA, for example, uses 3D printing to fabricate engine components and rocket nozzles. In one case, the agency successfully tested a 3D-printed injector for a rocket engine, which would have traditionally required over 200 parts but was reduced to just two components with additive manufacturing. This drastically reduces weight, assembly time, and potential points of failure.
Moreover, GE Aviation reported producing over 100,000 3D-printed fuel nozzles for its LEAP jet engines by 2023. These nozzles are 25% lighter and five times more durable than traditionally manufactured versions, proving the value of customization not only in design but also in performance.
The fashion industry has started integrating 3D printing to create made-to-order pieces that reflect individual tastes and body measurements. For niche fashion labels and designers, the technology removes barriers associated with fabric waste and unsold inventory.
Luxury fashion house Iris van Herpen pioneered the use of 3D-printed garments in haute couture, creating complex, futuristic designs that would be impossible using conventional sewing techniques. Similarly, startups like Zellerfeld are disrupting the footwear space with fully 3D-printed, recyclable shoes, custom-fitted to individual customers via smartphone foot scans.
This level of product personalization is reshaping consumer expectations and opening new avenues for eco-friendly and ethical fashion production.
In the realm of industrial operations, 3D printing is enabling factories to create custom jigs, fixtures, and tools that optimize workflows and enhance precision. These parts are often used in small quantities, tailored for specific production lines or testing processes.
German carmaker BMW has integrated additive manufacturing into its production plants to fabricate over 300,000 custom tools and fixtures each year. This approach has cut down tooling lead times from weeks to just a few days, improving flexibility and production uptime.
For niche manufacturers operating in sectors like robotics, electronics, or renewable energy, the ability to design and fabricate unique tooling quickly is a distinct competitive advantage.
Beyond technical flexibility, 3D printing offers a compelling economic case for small-batch manufacturing. Traditional methods often require large capital investment for molds and dies, which only pays off at high volumes. Additive manufacturing bypasses this, allowing for cost-effective short runs or one-off items.
A 2024 Deloitte study estimated that companies using 3D printing for custom parts in small-batch production could reduce overall production costs by 30% to 50%, depending on the complexity of the design and materials used.
This economic shift is particularly important for startups and specialized suppliers who operate in volatile or experimental markets where customer needs evolve rapidly and product lifecycles are short.
Niche industries often focus on sustainable practices, either by regulation or brand ethos. 3D printing supports this through material efficiency and local production, reducing both waste and carbon footprint.
Unlike subtractive manufacturing, which cuts away material to create a part, 3D printing builds items layer by layer, using only what’s necessary. This significantly reduces scrap rates. In aerospace and automotive sectors, companies have reported material waste reductions of up to 80% when transitioning to additive methods.
Additionally, decentralized production means products can be printed close to the point of use, minimizing transportation and associated emissions. This supports circular manufacturing models, where broken or outdated parts are simply reprinted rather than discarded.
The next phase in 3D printing’s evolution involves AI-driven design optimization, where machine learning algorithms can generate product geometries tailored to specific performance requirements. This will enable even greater levels of customization, particularly in sectors like biomedical engineering and advanced materials.
As smart factories integrate digital twins and predictive analytics, 3D printing will shift from a standalone process to a fully integrated production method within Industry 4.0 ecosystems. This will enhance its scalability and real-time adaptability, making it even more suitable for niche markets that value speed and specificity.
3D printing is no longer futuristic. It is now a practical solution transforming design, manufacturing, and distribution in niche industries. Its role in customization is expanding across healthcare, aerospace, fashion, and automotive sectors. It enables product variations once seen as too costly or technically difficult.
Niche players use additive manufacturing to stand out and deliver unique value. It blends personalization, agility, and cost-efficiency in powerful ways. Advances in materials and printing technology continue to broaden what can be customized. Innovation is being redefined—layer by layer.
Many modern 3D printing services offer scalable, on-demand production without upfront infrastructure costs. Cloud-based CAD tools and shared fabrication labs also lower the barrier to entry for smaller players.
Low-volume, high-complexity products such as custom prosthetics, drone parts, specialty tools, or personalized luxury goods gain the most from additive manufacturing.
Yes. 3D printing allows rapid prototyping and material testing, enabling quicker adaptation to changing regulations, especially in healthcare and aerospace sectors.
It allows iterative design and functional testing before committing to mass production, significantly lowering financial and operational risks for new launches.
It enables hyper-localized manufacturing, reducing dependency on complex supply chains and allowing faster time-to-market even in remote regions.
To participate in our interviews, please write to our IntentTech Media Room at sudipto@intentamplify.com