or call: +1 (845) 347-8894
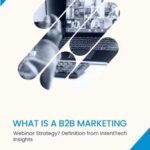
or call: +1 (845) 347-8894
Vitesse Systems is a leading provider of thermal management, antenna, and power distribution solutions for critical defense and space applications.
Vitesse Systems announced the completion of the installation of two additional additive manufacturing machines and the delivery of what it believes to be one of the largest additively manufactured satellite antennas in history. The antenna was designed, built, and tested at Vitesse’s antenna center of excellence in Longmont, Colorado. Vitesse leverages additive manufacturing to design and print antenna and thermal management solutions for a range of defense and space applications.
Richie Dart, General Manager, explained: “Additive manufacturing offers distinct advantages that we have been able to leverage to enhance the design of our offerings. Since installing our first additive machine in 2021, we have completely rethought our approach to designing certain types of antennas. This is particularly beneficial for space applications where mass and size are critical, and for ground applications where operating over a broad range of frequencies is increasingly important for both defense and civil applications.”
Top IntentTech News: Sonata Software Secures $73M AI Deal with US TMT Company
“We recently delivered our most complex space hardware to date. The antenna comprised 1,600 individual additive RF components. We were approached by our customer in 2022, who sought an antenna partner to support their satellite technology roadmap. By collaborating with our customers from the concept stage, we were able to leverage our space heritage and combine it with the benefits of additive manufacturing. This allowed us to reduce the overall size and mass of the antenna by 30%, optimize RF performance, and deliver the antenna in less than two years. Additive manufacturing builds the antenna layer by layer, which allows us to eliminate internal features that are only there for structural reasons. This not only improves RF performance but also reduces the mass and overall size of the antenna – a fundamental shift for satellite applications, allowing our customers to utilize available space and mass for other purposes.
For ground-based antennas, we have combined additive manufacturing with our existing antenna manufacturing processes. This allows us to design more capability into a single antenna, enabling our customers to communicate with airborne and space-based assets across a broad range of frequencies and orbits. Furthermore, our customers require solutions within increasingly shorter timeframes, often weeks, not months. Our additive capability, combined with our RF expertise and in-house testing capabilities, allows us to exceed our customer expectations.”
Top IntentTech News: Lucid and KAUST Partner to Boost EV and Autonomous Tech
Matthew Alty, CEO, added: “Expanding our additive manufacturing capacity is part of a broader investment strategy to meet the growing demand for high-performance antennas. Over the past few years, we have expanded our engineering, manufacturing, and test capabilities as the government has fundamentally changed how military programs are procured. Development timelines have been compressed, and performance requirements have increased as the connected battlefield has become a reality and the number of satellites and interconnected platforms has increased significantly. In response, we have had to rethink how we design, manufacture, and test our antennas. Additive manufacturing, combined with our in-house design and testing capability, allows us to significantly reduce the amount of time it takes from design concept to reality.”
Top IntentTech News: Rackspace startet OpenStack Flex für sichere Cloud
To participate in our interviews, please write to our IntentTech Media Room at sudipto@intentamplify.com
Source – PRWeb