or call: +1 (845) 347-8894
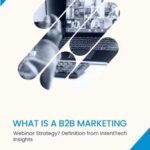
or call: +1 (845) 347-8894
or call: +1 (845) 347-8894
MACHINUM accelerates digital transformation and sustainability for manufacturing operations by optimizing shopfloor performance and productivity for industrial automation businesses
Siemens to demonstrate digitalization capabilities and how users can reduce their machining speed by up to 15% with new technology
Earlier this month, global technology leader Siemens announced its U.S. launch of MACHINUM at the International Manufacturing Technology Show (IMTS). MACHINUM is the CNC digitalization software portfolio designed to manage, analyze, and optimize shopfloor performance and aims to help machine tool users and builders improve their operations and productivity through seamless software integration.
The MACHINUM portfolio features Adaptive Control and Monitoring (ACM) which allows users to reduce their machining times by up to 15% and extend the life of their cutting tools, leading to greater manufacturing productivity.
Siemens
“It’s important for manufacturers to start or enhance their digitalization journey and MACHINUM can help optimize industrial automation operations at any scale,” said Dave Morley, mid-market sales manager, Siemens Digital Industries.
Dave added, “Siemens developed a digitalization portfolio that drives increased usability and capability, and at a lower cost, to provide greater access to this technology. Companies that can produce quality parts faster and more efficiently will continue to outcompete competition — and integrating MACHINUM can help do just that.”
The MACHINUM portfolio is built on three pillars:
Smart Machine offers lower programming and material costs, higher quality machine uptime and overall faster machining by using machine data for real-time, in-process quality control.
Smart Shopfloor provides customers with lower material, operational and programming costs, along with higher utilization, through more efficient preparation and pre-production resource management.
Smart Virtual Machine offers lower programming costs and higher quality and utilization for better machine engineering with the integration of digital twin and closed-loop engineering.
Each pillar enhances performance, allowing users to increase speed, agility and endurance of their operations. Within the Smart Virtual Machine pillar, companies can use digital twin to enable dependable virtual machining processes, accelerating the run-in of new parts and reducing costly downtime.
The digitalization portfolio is integrated into Siemens Xcelerator, allowing companies in the machine tool sector to facilitate digital transformation – making it more efficient, faster, and scalable in both manufacturing and design and the demand for energy efficiency, sustainability, and high-quality product manufacturing. The technology is not limited to SINUMERIK-controlled CNC machines, which allows the MACHINUM portfolio to be integrated into any existing manufacturing environment to future-proof the shop floor.
Source: Siemens Newsroom
More from Siemens:
Siemens Achieves Top 10 Ranking in TIME Magazine’s World’s Best Companies of 2024
Siemens + Global Battery Alliance | Focus on Eco-friendly Batteries
America’s Cup Teams Gain Edge with Siemens Digital Twin Technology
Siemens gifts USask | Supports Electronic Chip Design Software Research and Talent