or call: +1 (845) 347-8894
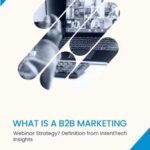
or call: +1 (845) 347-8894
or call: +1 (845) 347-8894
The face of manufacturing is undergoing a significant transformation. Factory automation, the integration of technology into production processes, is driving this change. At the forefront of this revolution lies robotics, with its potential to streamline production and propel businesses forward.
Factory automation has been around in the industry for more than six decades. It deals with the implementation of automation technology and systems. The main purpose of automation is to increase the productivity and efficiency of the systems by automating repetitive tasks in an industrial setup. Robotics is at the heart of factory automation.
In this article, we will evaluate the role of robots in factory automation with the help of use case scenarios.
The use of robots in factories is no longer science fiction. It’s a reality that’s rapidly changing the game. Here are some recent data related to the use of automation for factory work.
These numbers paint a clear picture: robotics is becoming increasingly vital in factory automation.
The integration of robotics offers a multitude of benefits for manufacturers, including:
Across diverse industries, robots are transforming factory operations. Here are a few real-world examples:
The future of robotics in factory automation is promising, with ongoing technological advancements poised to deliver even greater benefits to industries worldwide. Let’s explore these advancements in detail.
Collaborative robots, or cobots, represent a significant advancement in robotics. Unlike traditional industrial robots, cobots are designed to work safely alongside human workers, fostering a collaborative and symbiotic relationship between man and machine on the factory floor.
These robots are equipped with advanced sensors and algorithms that enable them to detect the presence of humans and adjust their movements accordingly to avoid collisions. By ensuring the safety of human workers, cobots open up new possibilities for automation in industries where close interaction between humans and machines is necessary.
Cobots assist with a wide range of tasks, from repetitive assembly operations to intricate precision tasks that require human-like dexterity. Their ability to work alongside humans enhances efficiency and promotes a more human-centric approach to automation, where technology complements and augments human capabilities rather than replacing them.
Artificial intelligence (AI) Integrating AI with robotics represents a significant leap forward in factory automation. By leveraging AI algorithms, robots can make intelligent decisions based on real-time data. As a result, they are able to adapt to changing conditions and perform more complex tasks with greater precision.
One of the key benefits of AI-powered robotics is their ability to learn from experience. By analyzing vast amounts of digital data from sensors, cameras, and other sources, AI-equipped robots can achieve higher performance ratings. Consequently, this adaptive learning capability enables them to optimize their movements, refine their strategies, and overcome challenges more effectively. Ultimately, this leads to increased productivity and enhanced quality in manufacturing processes.
AI also opens up new possibilities for predictive maintenance, where robots can detect signs of wear and anticipate potential failures before they occur. By proactively addressing maintenance issues, AI-powered robots minimize downtime and ensure uninterrupted production, saving time and resources for manufacturers.
Machine learning (ML) is another critical component of the future of robotics in factory automation. ML algorithms enable robots to learn from data without being explicitly programmed, allowing them to recognize patterns, make predictions, and adapt their behavior autonomously.
Robots equipped with machine learning can analyze data in real-time to identify inefficiencies, optimize processes, and make data-driven decisions on the fly. For example, in manufacturing, ML-powered robots can analyze production metrics to identify bottlenecks, adjust their workflows accordingly, and maximize throughput.
Furthermore, machine learning enables robots to adapt to changes in their environment autonomously. Whether it’s variations in product specifications, changes in production schedules, or unexpected obstacles on the factory floor, ML-equipped robots can adjust their movements and strategies to maintain optimal performance and efficiency.
While robotics offers significant advantages, there are also challenges to consider:
Robotics is undoubtedly revolutionizing factory automation. By offering increased productivity, improved quality, and enhanced safety, robots are empowering manufacturers to gain a competitive edge. As technology continues to evolve, the future of robotics in factory automation promises even greater efficiency, flexibility, and innovation for the manufacturing industry.